ODM Service Process
Your trusted OEM/ODM partner for premium glassware manufacturing — built on precision, quality, and flexibility.
Initial Consultation
Client Input:
Product categories (wine glasses, dinner plates, etc.), material (soda-lime glass), design style, order quantity, target market.
→ Our Support: Technical guidance (heat resistance, thickness, processes), market insights.Requirement Finalization:
Key specs: dimensions, capacity, color, surface treatments (patterns), packaging.Quotation & Contract:
Pricing based on process complexity, material costs, MOQ.
Contracts: NDA and service agreement with delivery timelines & payment terms.
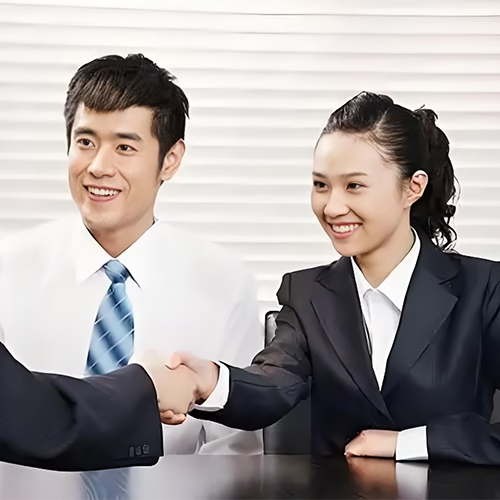
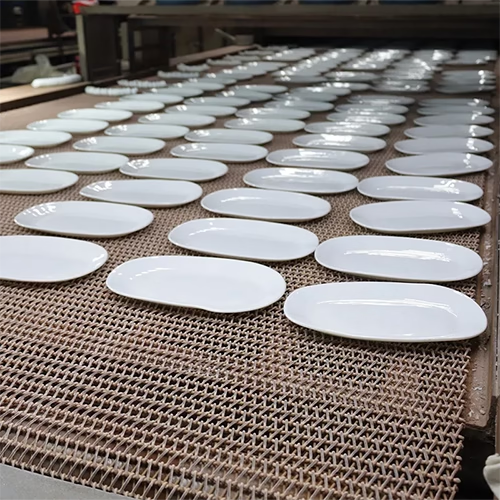
Design & Sampling Process
Design & Development
ODM: Provide original designs (3D models, renderings, reference samples).
OEM: Evaluate client designs, optimize production feasibility.Sample Production
Create 1–3 sample batches using mass-production processes.
Submit test reports (impact/thermal resistance, dimensions).Confirmation & Adjustment
Client tests samples, feedback → Revise until final approval.
Design & Sampling Process
Tooling & Line Setup
Custom molds (for exclusive designs), schedule production lines.
Procure raw materials (quartz sand, soda ash) & accessories (packaging, labels).Trial Production
Produce 100–500 trial units to validate process consistency & efficiency.
Secondary QC checks, submit trial report → Client approval triggers full-scale production.
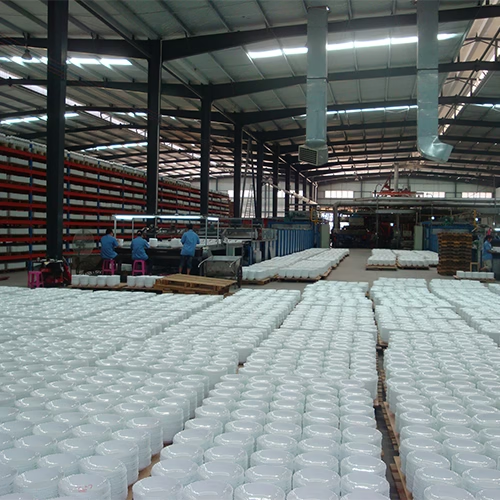
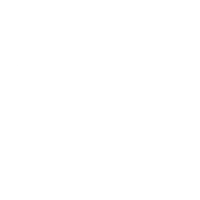
From concept to finished product, we offer full design and manufacturing support tailored to your brand’s needs.

Our samples undergo real production processes and rigorous testing to ensure market-ready quality and performance.

Clear communication, fast feedback loops, and adaptable processes ensure efficient and reliable project execution.
Mass Production & Quality Control
Full-Cycle Production
Process: Glass melting → Forming (blowing/pressing) → Annealing → Cooling → Surface finishing (cutting/polishing) → Printing/engraving.
Key Controls: Real-time monitoring of annealing temperature, forming speed, and mold precision.Multi-Layer Inspection
In-line QC: Bubble/impurity detection, thickness uniformity, edge smoothness.
Final QC: Full inspection (appearance/dimensions) or AQL sampling (strength/packaging integrity).

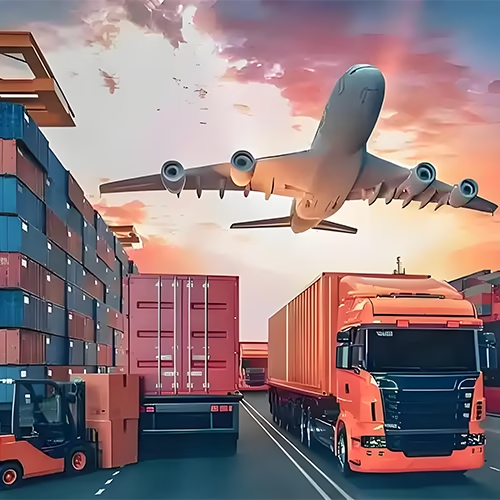
Logistics & Delivery
Custom Packaging
Eco-friendly paper boxes, luxury gift boxes, shock-absorbing foam inserts (EPS/EPP).Logistics Coordination
Support FOB/CIF/EXW terms; provide customs documents (COO, QC reports).Delivery Tracking
Real-time tracking IDs; post-sale team monitors delivery confirmation.
After-Sales Support
Quality Assurance
Free replacement for non-human damage during the warranty period.Repeat Orders & Upgrades
Prioritized production scheduling for repeat orders.
Support design iterations and process upgrades (e.g., material optimization, functional enhancements).
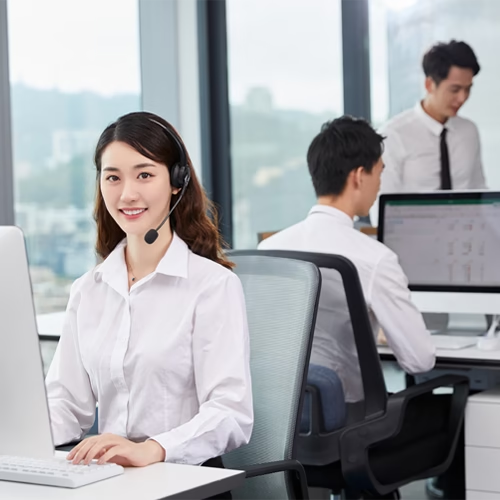